My techs seem to be busy all day. Why are we barely keeping our heads above water?” If you’ve thought or said this out loud, you’re not alone. The rising costs associated with running an automotive shop these days are making it increasingly difficult to keep the doors open. But by regularly evaluating workflow practices, shops may find some ways to fight those shrinking profit margins.
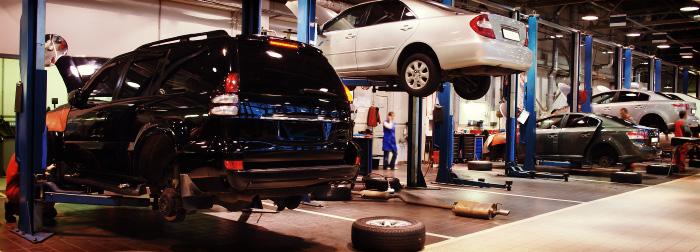
First, let’s quickly define the difference between two of our industry’s benchmark financial indicators – efficiency and productivity. Efficiency is a measurement of a tech’s ability to complete a job in a prescribed amount of time. For example, if a job’s flat-rate time is one hour and the tech takes one hour, he’s 100 percent efficient. Productivity is based on the number of hours the tech is on the clock compared to the billable time he flags each day. To be 100 percent productive, the tech will have to flag at least 40 hours in a 40-hour work week.
When we look at low productivity, there are a few issues that can typically be identified. The problem may lie with the tech’s lack of efficiency but more often, the issue is the shop’s ability to provide techs with what they need to be productive. Let’s identify some of the leading shop practices that can cause low productivity:
- Poor description of symptoms from the service advisor
- Lack of reliable diagnostic and repair information
- Lead techs spending too much time assisting apprentice techs
- Lower skill-level techs being dispatched higher skill-level work
- Techs idle while waiting for parts
On the Service Drive
Service advisors and techs can use the inspection forms and checklists included in ALLDATA Repair to ensure they are asking the right questions. ALLDATA Repair includes checklists for engine performance, air conditioning and many other systems. Non-subscribers can register for a free trial to take advantage of the many benefits of using checklists, including:
- Leads to more accurate repairs and fewer come-backs
- Helps techs develop a logical diagnostic strategy early in their diagnostic process
- Gives techs a more complete and accurate picture of the problem (What, When, Where)
- Builds credibility with the customer to use guided professional questions
- Bonus: can lead to additional service recommendations
In the Shop
Reliable diagnostic and repair information is essential for both efficiency and productivity. Every shop should have electronically-delivered OEM diagnostic and repair information available for techs. With increasing regularity, manufacturers are enlisting computers to operate and monitor all vehicle systems. Some vehicles require that, after a simple brake pad replacement, certain control modules need to be programmed to recognize the new pads. These days, there are not many diagnostic, service or repair procedures that can be successfully completed without OEM reference information.
Most shops usually charge one hour for diagnostic time—but not all problems can be diagnosed in one hour. If a tech is struggling with a diagnosis, it’s important to ask for help before reaching the end of that diagnostic time. An efficient, reliable resource can help develop a sound diagnostic strategy or give them a new perspective. Internet searches or calling techs in other shops for advice can take too much time and can be inaccurate. There are more dependable resources of information.
Techs, you can post problems, symptoms and the tests performed on a trustworthy automotive forum for professional techs. Chances are, one of your peers has encountered the exact problem that’s giving you grief and will be happy to tell you how to diagnose and fix it.
Asking for help and advice from a diagnostic hotline service can result in getting the vehicle back to the customer more quickly. While most shops are lucky to see three or four diagnostic problems a week, the techs who work on diagnostic hotline services are involved with 10-15 diagnostic problems every day. They help techs from all over the country diagnose and repair vehicles, so they likely have the answer to your exact problem.
The skill level of your technicians can have a big impact on efficiency and productivity. It’s a good idea to have techs at different levels, so work can be distributed to the most efficient person for the job. While it’s good for less-experienced techs to shadow and learn from your pros, that can slow them both down—and mean it takes longer for your customers to get their vehicles back. Finding the balance between teaching, learning and working is important. Techs of all skill levels can benefit from services like diagnostic hotlines to speed diagnosis and repairs—and hotlines can help less-experienced techs get up to speed quickly to handle more challenging repairs.
Finally, inventory can have a big impact. Whether it’s maintenance or repair-related, a timely supply of high-quality parts to finish the job can directly affect productivity. Many shop management systems incorporate electronic parts ordering that will seamlessly populate estimates with part numbers and prices. Some other benefits of ordering parts online are: faster delivery times, increased order accuracy, 24/7 availability and a wider selection of brands. Don’t let lack of parts inventory or slow delivery slow your vehicle turnaround—this is a simple one to fix.
Techs, Be Masters of Your Own Efficiency
Automotive technology is constantly evolving, and so should you. Commit to learning new systems and diagnostic strategies, such as network communications and drivability diagnostics. The more you learn, the more you’ll earn. And finally, one more efficiency booster, which is basic but bears repeating. Buy professional-grade tools and diagnostic equipment. Specialty tools, especially high-quality scan tools, are a “must have” for every tech. Develop a strong, ongoing relationship with your tool truck guy. That relationship will last at least as long as your career. And those quality tools will speed diagnosis, repairs and customer vehicle delivery—positively impacting your shop’s bottom-line.
ALLDATA offers a variety of products that can help improve efficiency and productivity. From ALLDATA Repair’s OEM-accurate information and checklists to help streamline diagnosis and repairs; to Tech-Assist’s team of ASE Certified Master Technicians who are available to help with tough diagnoses and repairs with just a phone call; to ALLDATA Manage Online’s streamlined shop operations, from scheduling appointments and assigning techs to jobs to ordering parts from multiple online catalogs and auto-populating invoice information—we are here to help you.
Watch the 3 Secrets to Auto Repair Shops on our webinar page to learn more about how ALLDATA can help improve your shop’s productivity and efficiency. And let us know if you’d like a product demo or free trial of the ALLDATA solutions that best fit your shop’s needs. if you wish to try ALLDATA Repair please click here to start your free trial.
About the Author Rich Diegle, ALLDATA Tech-Assist Team supervisor, has over 40 years of industry experience with over 10 years of automotive marketing and editorial experience.
Want to see how ALLDATA can improve shop efficiency? Check out our suite of products, each designed to contribute to both shop efficiency and productivity.
If you would like to read more articles like this one please subscribe to ALLDATA News.
